Engine Cooling
- Nev
- Nov 10, 2022
- 2 min read
Updated: Dec 12, 2022
Due largely to the Amateur built/Experimental category of the Bearhawk, there is no one standard for engine cooling.
Factors affecting engine cooling
Most cowlings are designed with a high pressure area above the cylinders and a low pressure area below the cylinders, which combine to draw cooling air through the cylinder head fins. Any additional air requirements drawn from the baffles above the cylinders will reduce the pressure in that area, and lead to an increase in CHT's. This includes things such as airflow for the oil cooler, heater muffs, ignition cooling etc.
Additionally, any outside air that can access the lower cowl without passing through the cylinder fins tends to increase the pressure in the low pressure area, and reduce the cooling air flow.
One example is adding an additional heater. This draws additional air from the high pressure area leading to an overall reduction in pressure differential. Lower cooling airflow leads to higher CHT's, which may limit the cruise speed at low altitudes/higher ambient temperatures. It becomes particularly noticeable at high AOA/low airspeeds, when there is less cooling airflow and every last drop is helpful.
Engine Run-in
It is common (and normal) for builders to experience high cylinder head temperatures and high oil temperature during engine run-in. I quickly realized that by operating with the throttle wide open in level flight, the airflow (due to the higher speed) kept the CHT's right on the upper limit and I was able to modulate them while still at a very high power setting.
Normal Flight
There are two main methods to assist in engine cooling currently used.
Cowl Flaps
Cowl flaps are a moveable flap under the lower cowling, controlled by a cockpit lever. When opened they protrude down into the airflow creating a low pressure that helps to draw air through the engine compartment. When opened they also increase the outlet area. They offer the advantage of creating more cooling during high power demands, particularly at high AOA and slow airspeed.
Cooling Air Exit Lip
Many builders - myself included - simply attach a cooling air exit lip that protrude approximately 2" (50mm) below the cooling air exit. The lip protrudes into the airflow and lowers the air pressure, drawing more air through the engine compartment. The effect is very noticeable. It does also generate drag, so there will be a small airspeed penalty.
Other things that made a noticeable difference to lowering the temperature on my engine:
- Advancing the ignition to the correct setting (it was initially not set correctly) lowered the CHT's and EGT's significantly.
- Installing a small curved lip at the bottom of the firewall helped. This smooths the exit airflow.
- Running the engine LOP always lowers the temperatures. (However I didn't do this while running the engine in).
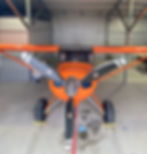
